Case Study
Johnny’s Selected Seeds
Johnny’s Selected Seeds is a seed producer and merchant headquartered in Maine, USA. The company has grown from a fledgling business to an international multichannel retailer. New technical limitations led its warehouse operations team to adopt manual processes. With more than 10,000 products dispersed across a 25,000-square-foot warehouse, the company needed a more robust solution, and we puzzled it out.
FoodTech
2017-2018
Services
Project Management
Experience Design
Agile Development
Software Architecture
QA
Technology Used
Java
ReactJS
Redux
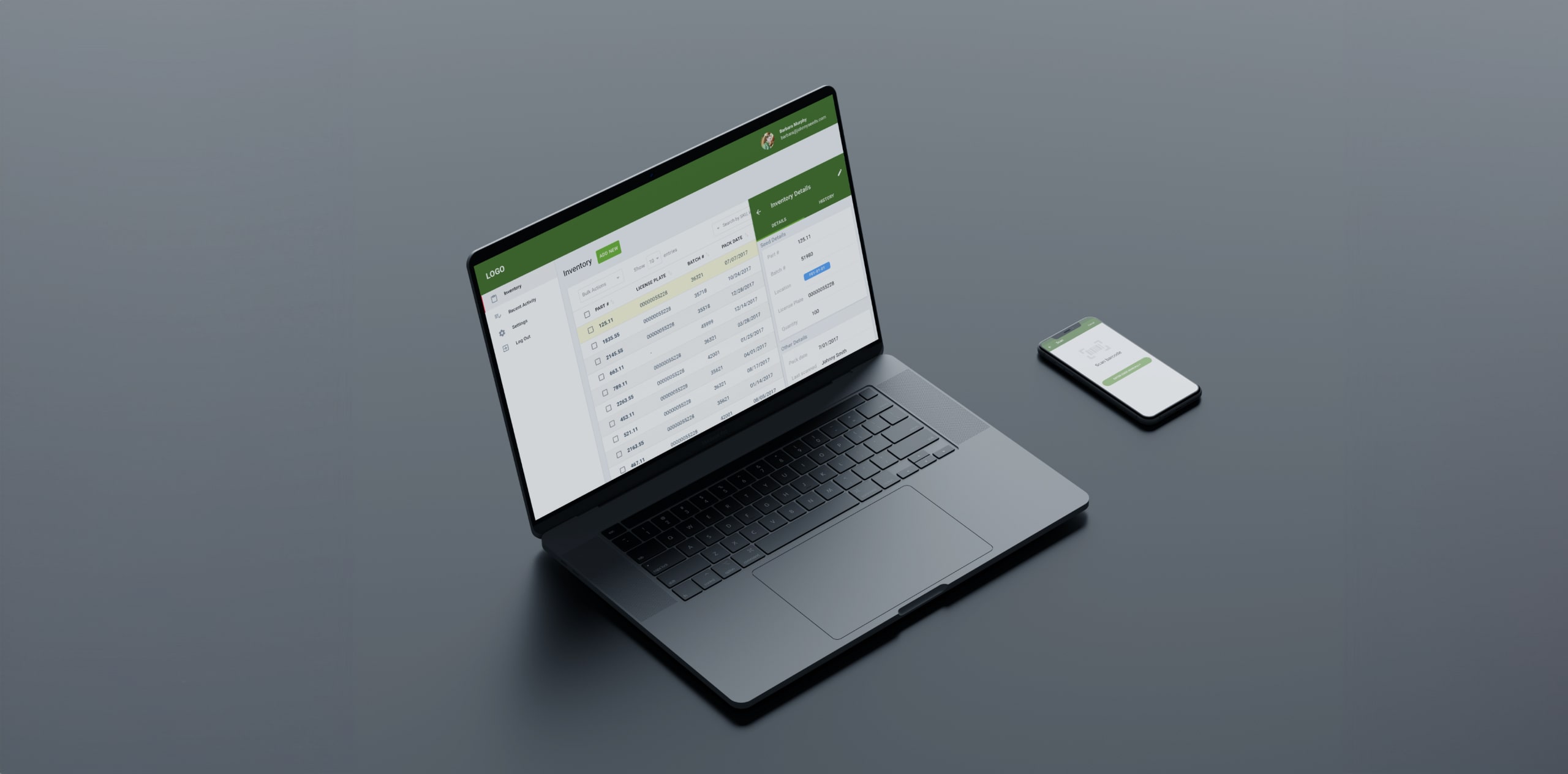
Client feedback
“One of the more common questions I’ve heard is “Is that it? That seems too easy.” That is an excellent problem to have and shows how everyone put a lot of thought into how the application should function from both a user and backend perspective”
IT Project Manager
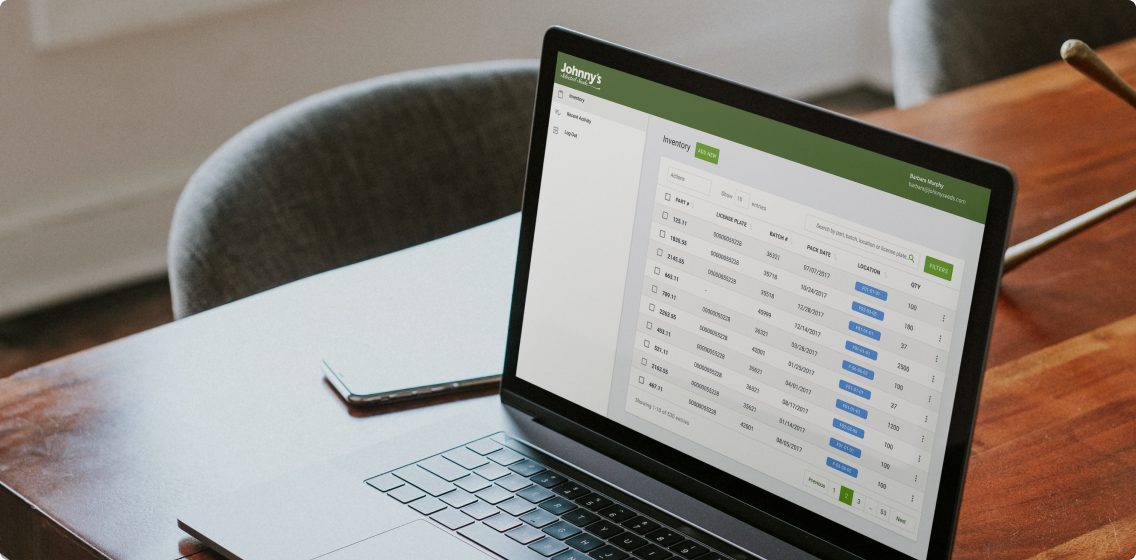
Challenges
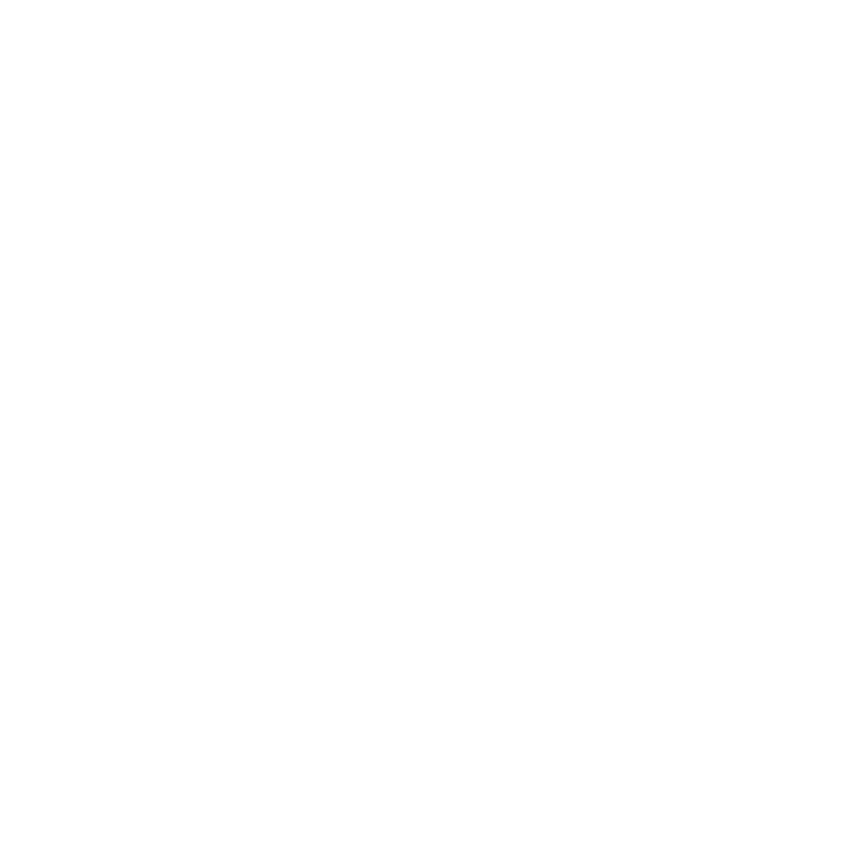
Lack of flexibility to handle unique business needs.
Johnny’s Selected Seeds learned that large-scale warehouse management systems lacked the flexibility to handle their unique business needs.
Incremental system changes and search for a new custom solution.
There was a need for Johnny’s to make incremental system changes, which led the company to seek a custom solution for the project.
Outdated manual processes leading to user dissatisfaction.
Without a digital movement history and chain of custody, the warehouse team had to spend more time tracking down missing products and less time fulfilling orders and ensuring quality customer service.
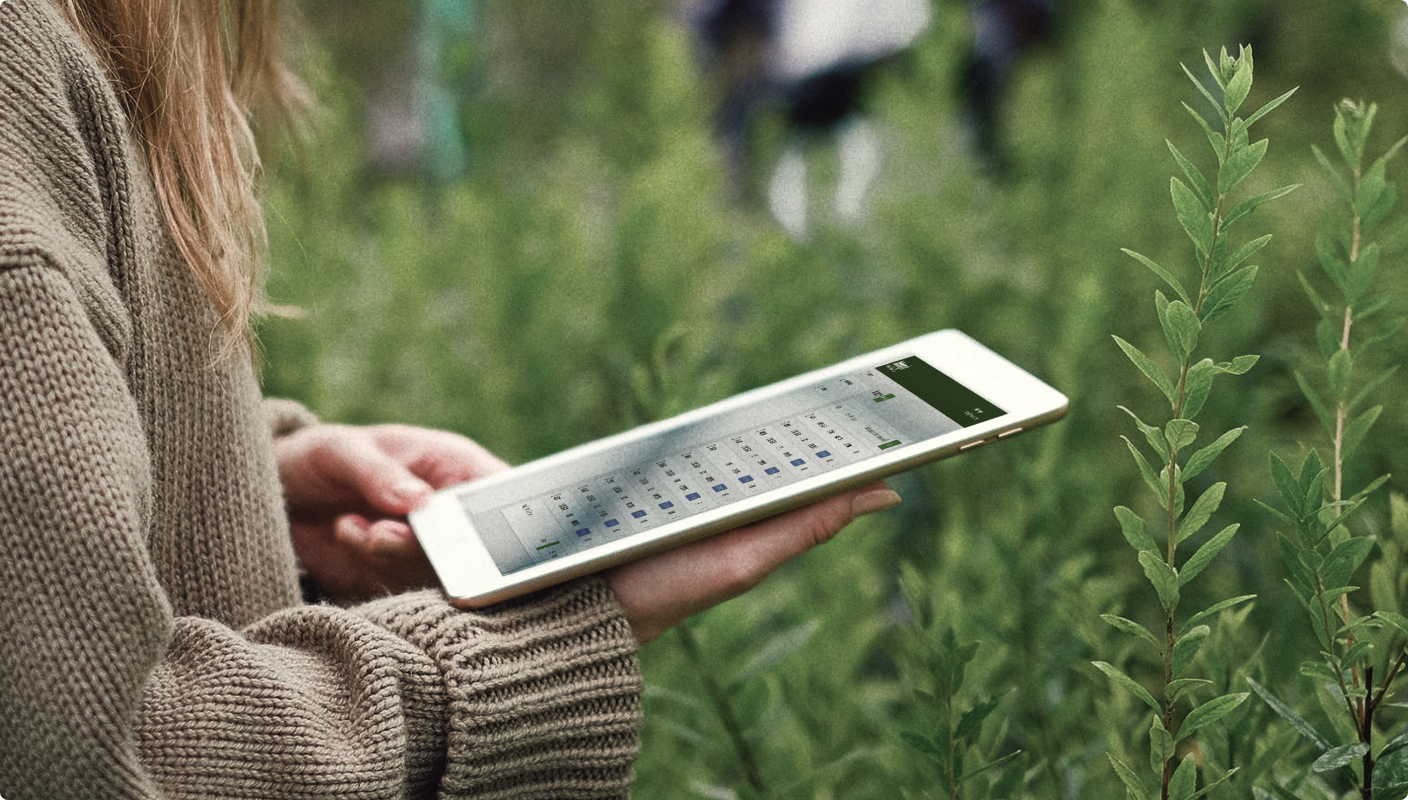
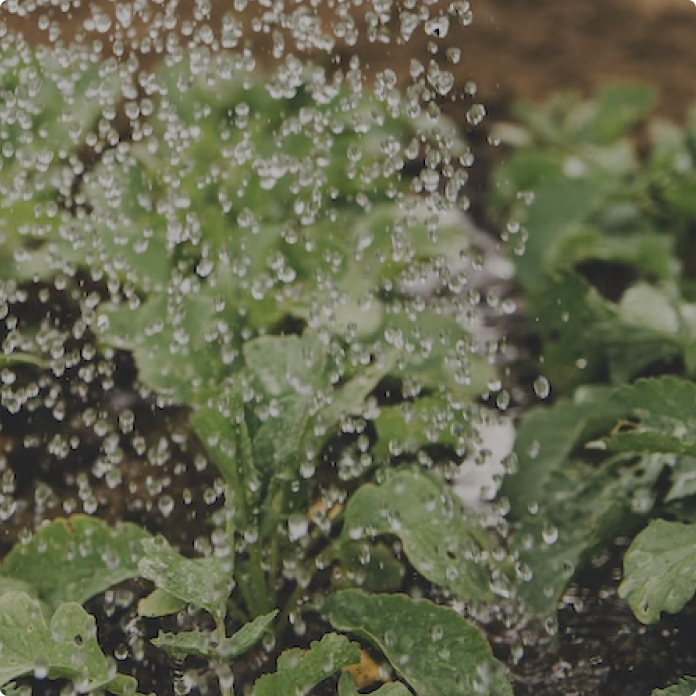
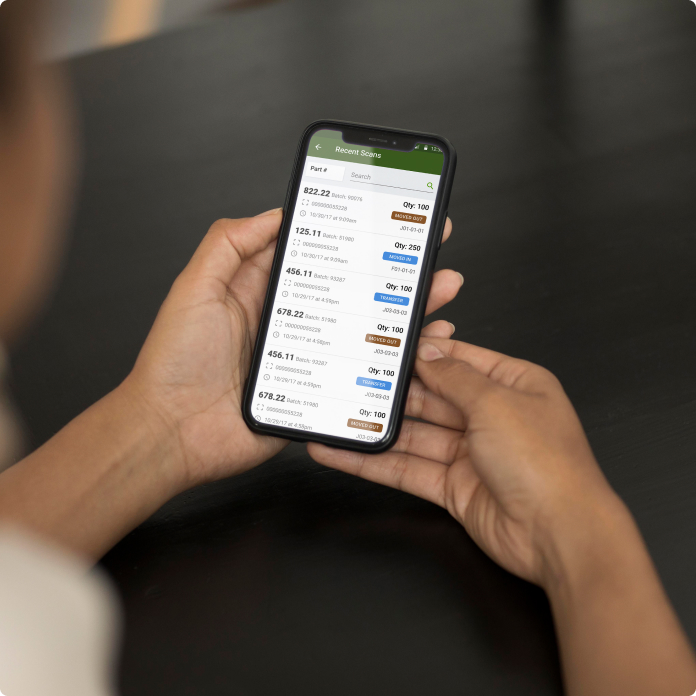
Solutions
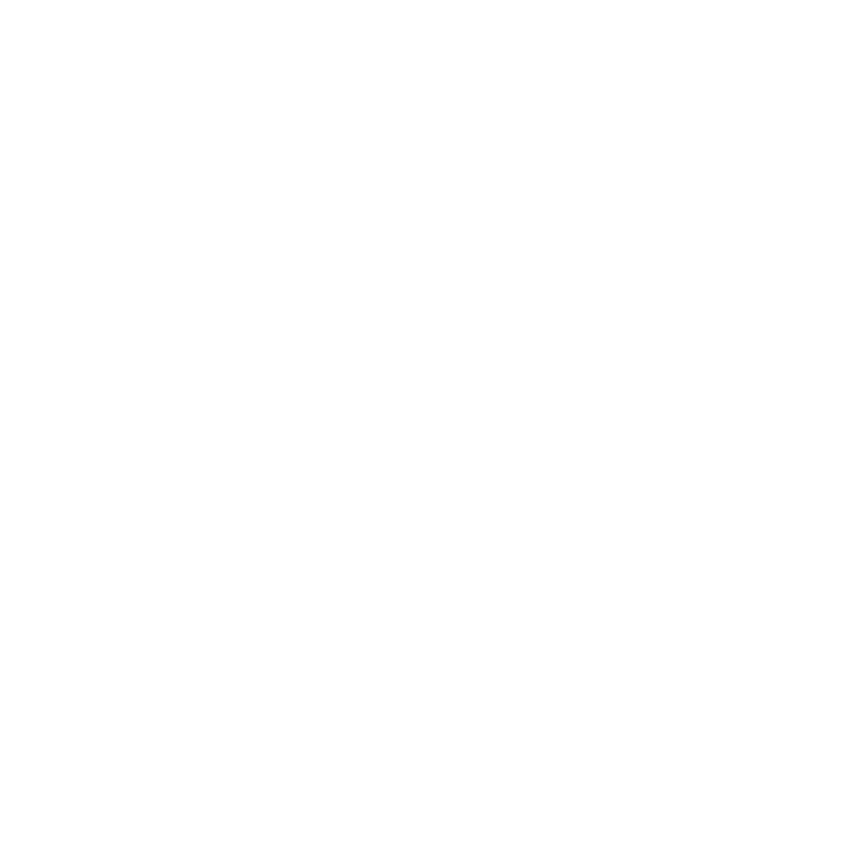
Design thinking techniques implementation to understand target users, workflow, and pain points.
We interviewed the front-line warehouse employees to adopt an automated real-time system, including increased productivity, reduced user error, and better data integrity.
RFID-compatible Android app in Java and complementary web app in ReactJS.
We built the RFID-compatible Android app in Java to provide faster development and easier integration with the hardware. We also built a complementary web app in ReactJS.
Close communication with Johnny’s team for better performance.
Our developers worked closely with Johnny's in-house development team to design and implement the data model, integrate the API, and support single sign-on.
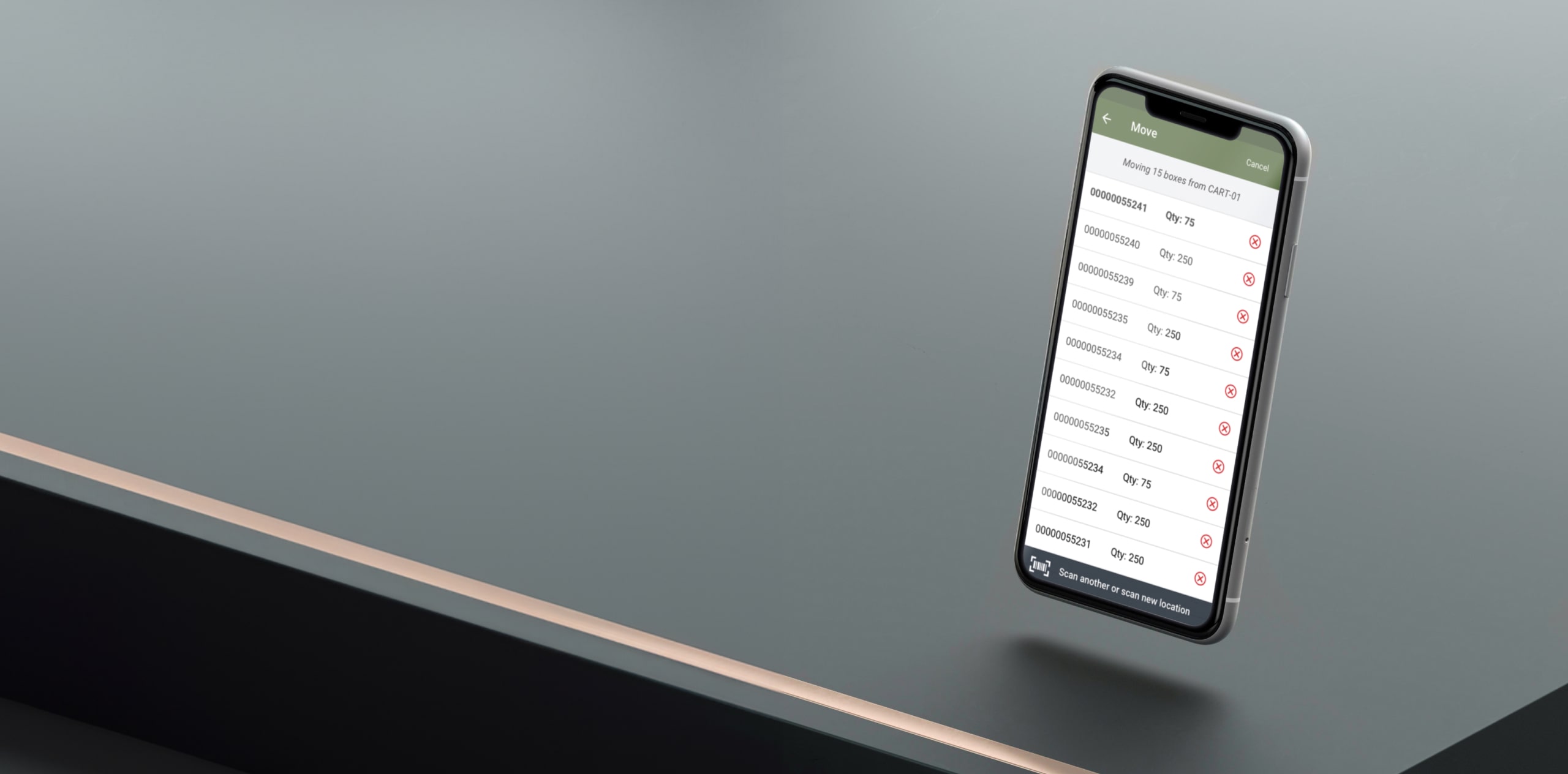
Results
Hire usOptimization for quick repetitive transactions.
We achieved better performance with a native app to ensure fast order fulfillment, minimize the necessary inputs and increase user transaction speed while conducting high-frequency, repetitive transactions.
Real-time inventory movements.
Users can now complete inventory movements in real-time on a mobile device instead of hand-written tracking and delayed data entry to head into their busy shipping season with confidence.
Improved work management within the team.
With over 50% of the workforce being seasonal hires, a simple user experience with a short learning curve helped reduce reliance on a handful of key team members.
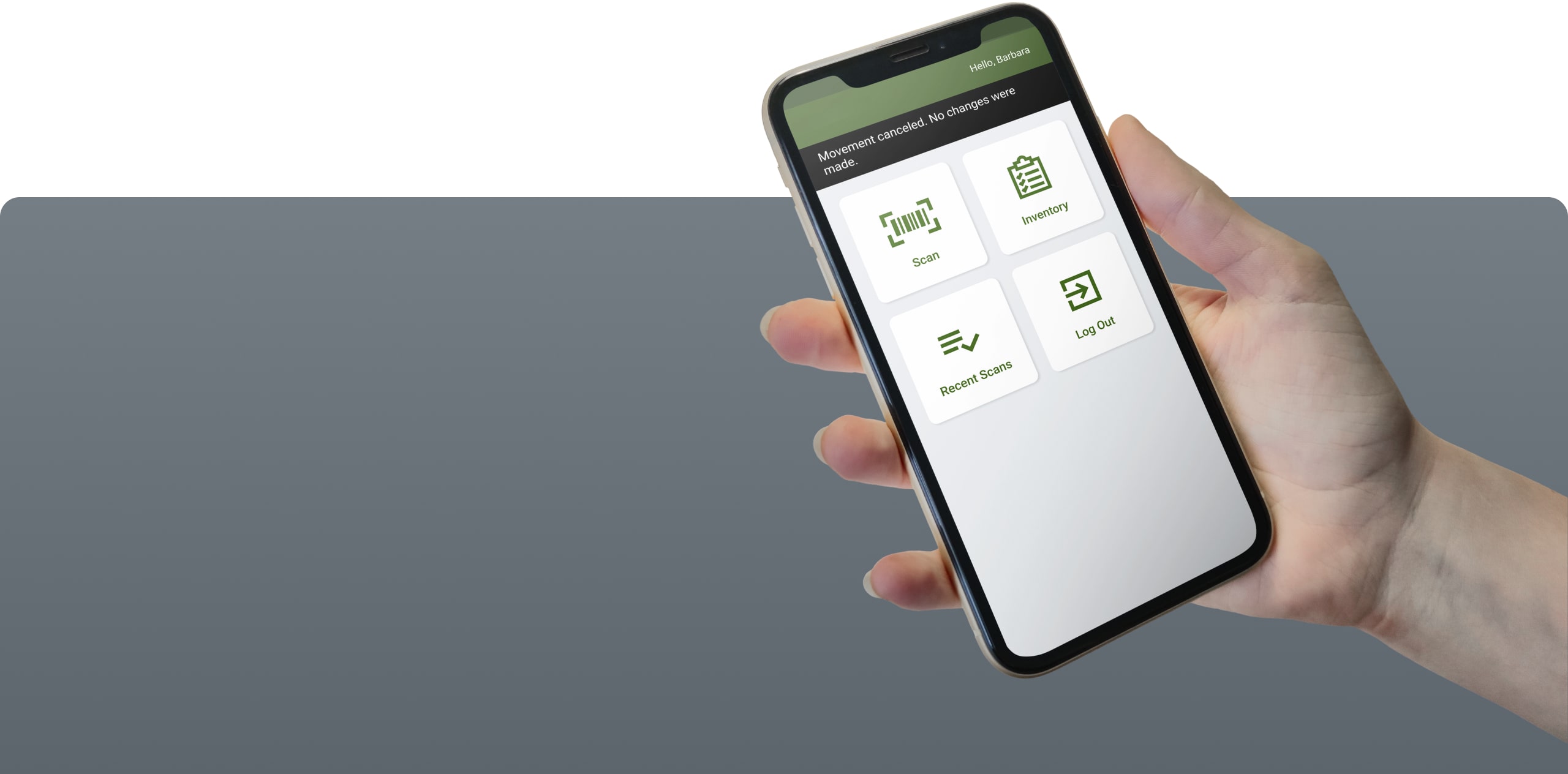